telescope primary mirrors
Whether on the ground, airborne or space-based, telescope designs are calling for larger and larger light collection capabilities. To meet the challenging requirements, primary mirrors designs are pushing the limits of manufacturability. Mirrors are being produced as either monolithic structures cast from a single piece of glass, or as segmented systems consisting of many smaller mirrors that focus the light collectively.
In either case the challenge from a manufacturing standpoint is to build the most stable, lightweight, and high-resolution optical system possible, which requires some of the most advanced metrology available today.
Measuring monolithic mirrors
Monolithic primary mirrors are cast from single blanks of glass, which are then ground to their final concave shape, polished and coated to specifications.
Such heavy optics demand sturdy and rigid support structures, a constraint which typically limits their use to ground-based telescopes. To reduce the structural demands, these mirrors are typically lightweighted in some fashion, by implementing a honeycomb of voids behind the mirror, employing a sandwich construction, etc. Through the use of these techniques, manufacturers are able to produce monolithic mirrors to diameters as large as 8 meters for the world’s premiere telescope projects.
The overall shape, waviness and roughness of these mirrors must be verified throughout manufacturing to guide the polishing process and to ensure final performance. The mirror must also be tested over the range of orientations it will experience in use, to understand how its shape will change as gravity loads change. Large radii of curvature require the measurement instruments to be placed many meters (or tens of meters) from the mirror. The distance introduces substantial vibration and turbulence which renders standard phase-shifting interferometers unusable. In some cases, when several monolithic mirrors are used as segments of a single primary (as in the Giant Magellan Telescope, GMT), aspheric shape may be introduced, further complicating the measurement process.
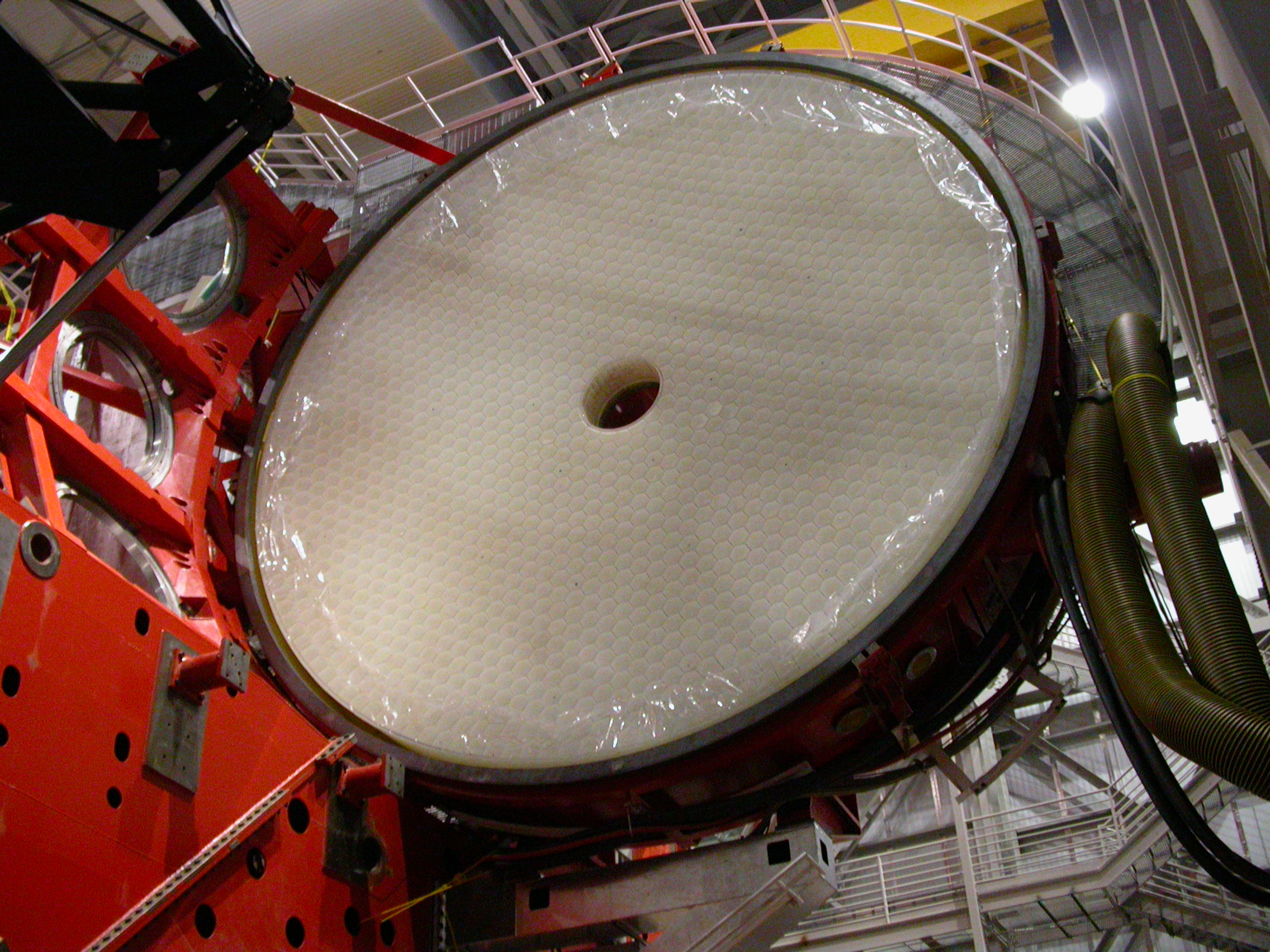
Measuring segmented mirrors
Monolithic mirrors are typically too heavy for airborne, space-based, and large terrestrial telescopes. For these applications, primary telescope mirrors are designed with many smaller mirrors segments which together equal the light gathering of a single, large mirror. An example is the European Extremely Large Telescope (ELT), which, when complete, will use nearly 800 hexagonal segments for its primary mirror. The weight savings with a segmented primary mirror is enormous, though the complexity of manufacturing and aligning the segments can introduce a new set of challenges.
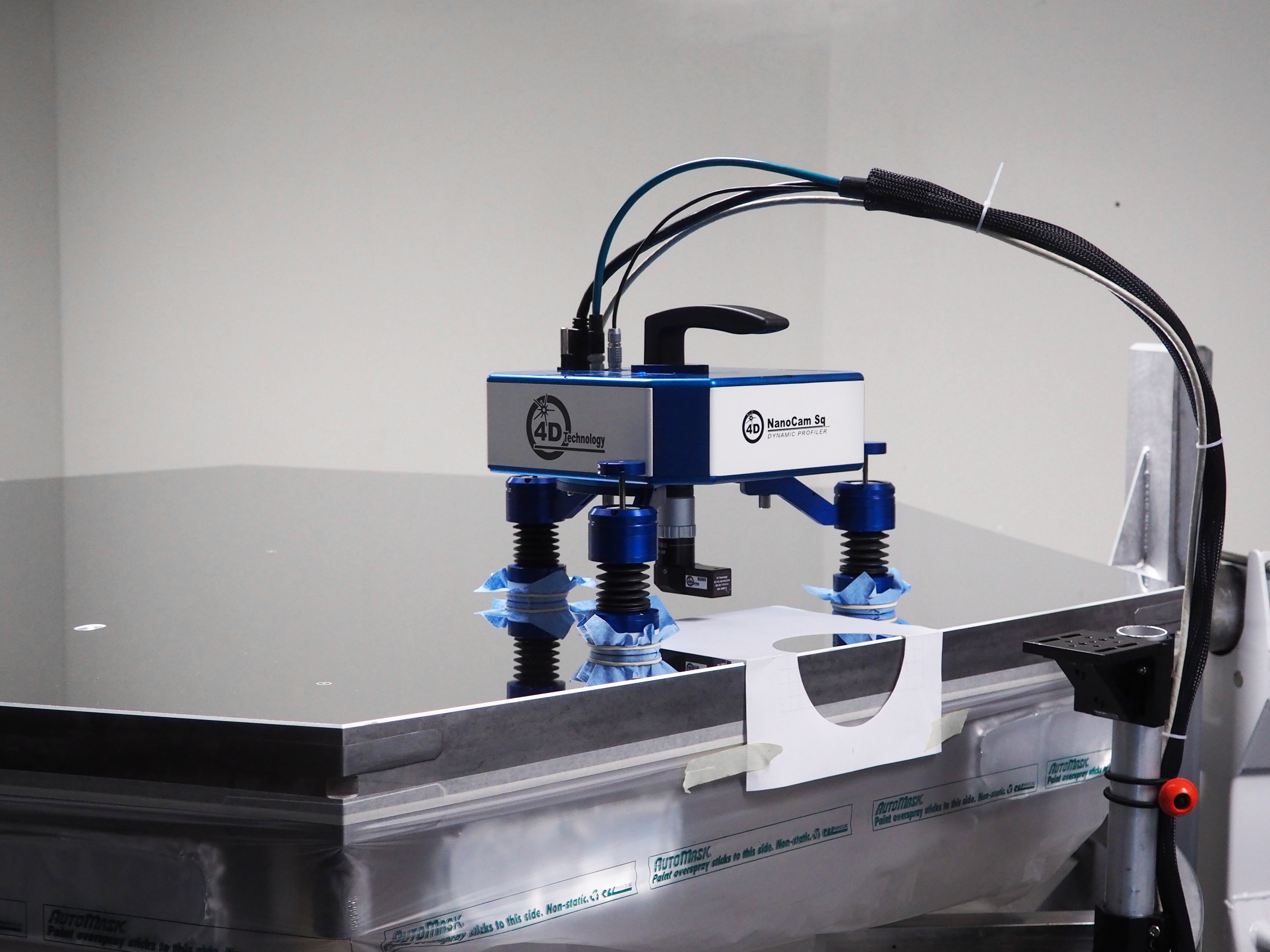
4D PhaseCam Twyman-Green interferometers are the industry standard for measuring concave primary mirrors and hexagonal mirror segments. PhaseCams offer several important advantages over more traditional Fizeau instruments:
- Vibration-insensitive measurement enables use in challenging environments such as cryo-vac testing or over long measurement paths
- The design can be extremely compact, enabling use in tight spaces, or in difficult-to-access locations
- The on-axis design provides excellent accuracy, particularly when measuring spherical elements
- The ratio of power between test and reference is adjusted in a lossless fashion.
NanoCam HD surface profilers excel at measuring surface roughness for small and large mirrors. The portable NanoCam HD can be placed directly on a mirror or segment for measurement. It can also be chucked on a robotic positioner or gantry to measure anywhere on a large mirror, or mounted inside a segment polishing system to guide the operation.
4D’s unique PhaseCam MW makes it possible to align mirror segments to sub-wavelength tolerances. This ability was critical to ensuring that the James Webb Space Telescope will be able to deploy and align its mirror components following launch.
Added Technical Resources
Optical Metrology for Space and Terrestrial Telescope Optics
A paper that explores how Dynamic Interferometry measures in adverse conditions, providing in-situ feedback and that allows for faster, more confident production of large mirrors and space-based optics.
Measurement of Space Optics and Structures
An overview of the techniques and configurations used to build dynamic interferometers and measurement results for a variety of space-based optical components as well as the structures that hold them under simulated space-flight conditions. These techniques and configurations have applicability for many non-space applications as well.
Products for Primary Telescope Mirrors
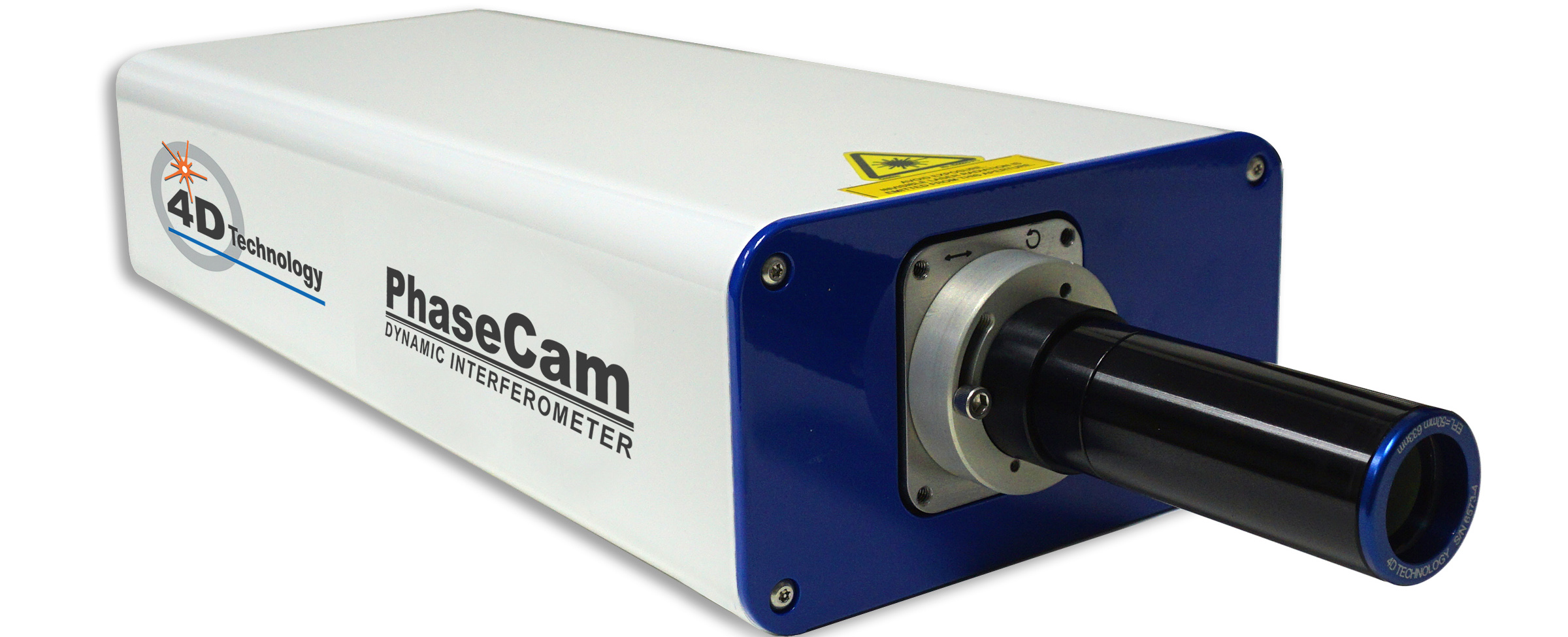
PhaseCam
PhaseCam Dynamic Interferometers are the industry standard for measuring concave primary mirrors and hexagonal mirror segments.
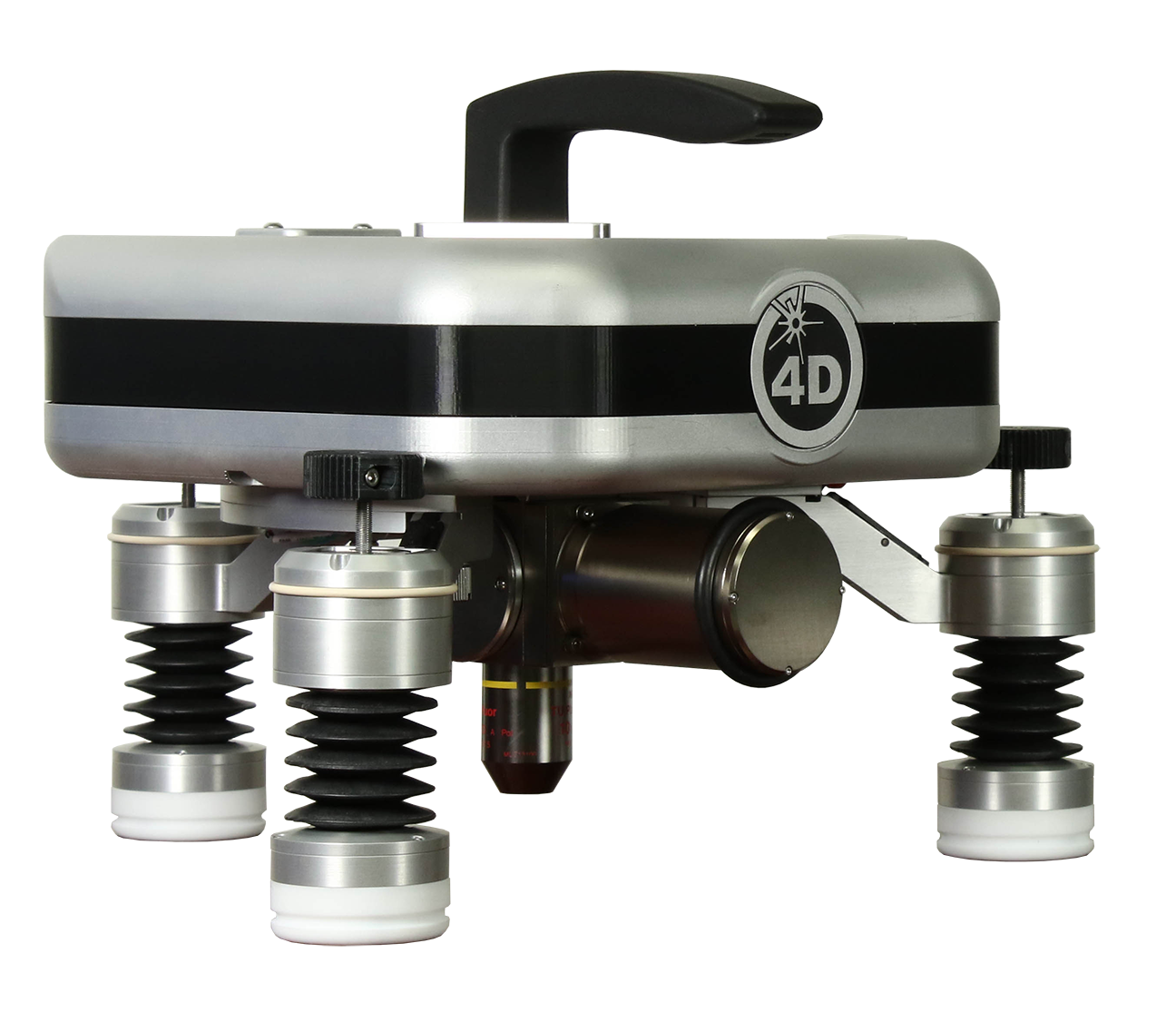
NanoCam HD
NanoCam HD surface profilers excel at measuring surface roughness for small and large mirrors. The portable NanoCam HD can be placed directly on a mirror or segment for measurement. It can also be chucked on a robotic positioner or gantry to measure anywhere on a large mirror, or mounted inside a segment polishing system to guide the operation.
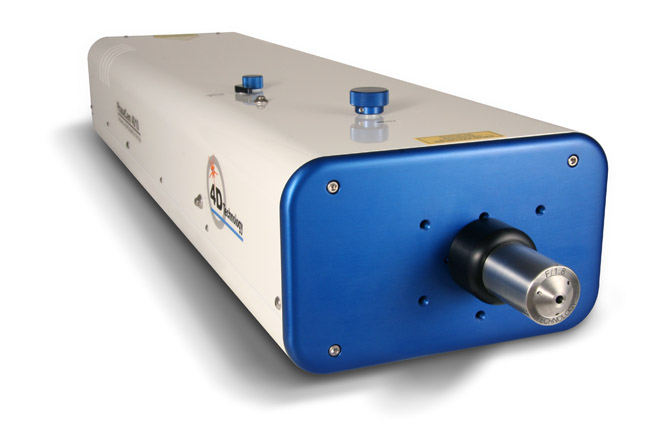
PhaseCam MW
PhaseCam MW makes it possible to align mirror segments to sub-wavelength tolerances.
Get In Touch
(520) 294-5600
Location
3280 E Hemisphere Loop, Ste 146
Tucson, AZ 85706
4Dinfo@ontoinnovation.com
Office Hours (Arizona Time)
Mon: 8am – 5pm
Tue: 8am – 5pm
Wed: 8am – 5pm
Thur: 8am – 5pm
Fri: 8am – 5pm
Sat: Closed
Sun: Closed
Send a Message